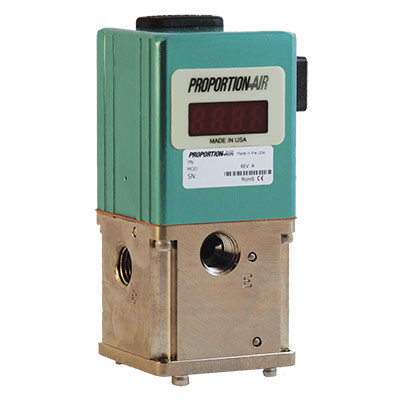
Both electropneumatic pressure regulators and flow control valves can be utilized in controlling vacuum systems. By using an electropneumatic pressure regulator, the designer develops a system which the suction force of the vacuum cup can be precisely controlled. The function of the electropneumatic flow control remains the same when controlling the flow of air in the circuit; thereby also controlling the speed at which the object is drawn into the vacuum cup.
Controlling the vacuum force is done through one of three different circuit designs. The first is the in-line method which uses a dedicated vacuum generator and vacuum regulator to produce a negative pressure. A vacuum transducer at regulator output provide feedback to the controller. The electropneumatic pressure regulator then adjusts the amount of force the vacuum pump applies to the object being lifted.
The second method generates vacuum using positive pressure through a venturi orifice. As with the in-line method, a vacuum pressure transducer is a critical input.
The final method, a vacuum breaker circuit, utilizes a vacuum regulator and a vacuum generator. The vacuum regulator controls the air allowed into the vacuum line to maintain the vacuum level. Like the first two methods, the vacuum pressure transducer is required.
Finally, achieving vacuum with an electro-pneumatic flow control valve is more straight-forward. Once the object is secured, installing a flow transducer in-line with the vacuum cup helps to reduce the flow. This allows for improved efficiency of the system by reducing air consumption that otherwise would be vented to the atmosphere as excessive by-pass. Not exhausting this air provides additional ergonomic advantages by reducing noise generation.
Filed Under: Air Preparation & Regulation, Engineering Basics, Pneumatic Tips