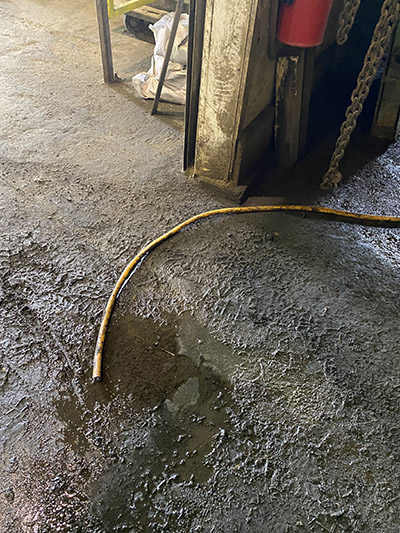
A wood products company had a two-compressor system installed on a mezzanine. Under the compressors and dryers were the piping and storage receivers. Each tank and each compressor had timer drains installed to expel the condensate that forms when the compressed air cools in the compressor aftercooler, piping, and storage vessels. The outlets of these drains were left to drain onto the compressor room floor.
A compressed air auditor examined the compressor room and found the condensate was collecting at points ankle deep on the compressor room floor. The compressors were screw type of lubricated design, so within the condensate was a small amount of compressor lubricant. After years of operation, the floor had become an oily mess, very slippery, creating a safety hazard — and what was worse was that the excess water was draining off through a storm drain that ran directly outdoors, polluting the general area.
The auditor pointed out that environmental rules prevented the release of lubricant to the environment, meaning that the plant was breaking the law, but there were solutions available. Most compressor suppliers can provide skimmer systems that can process the condensate and remove the lubricant. Further to this, typically a sump system is installed in compressor rooms to collect the condensate — and pump it to a collection vessel where it can be disposed of in an environmentally responsible manner.
This disposal system was upgraded and so, too, were the timer drains that were wasting valuable compressed air. The local utility provided an incentive to upgrade the drains to timer style and save energy. In all, the compressor room is now cleaner, drier, and more efficient.
Filed Under: Air Preparation & Regulation, Compressed Air Technologies, Pneumatic Tips